Electronic Shelf Labels Boost Efficiency in Healthcare Clinics
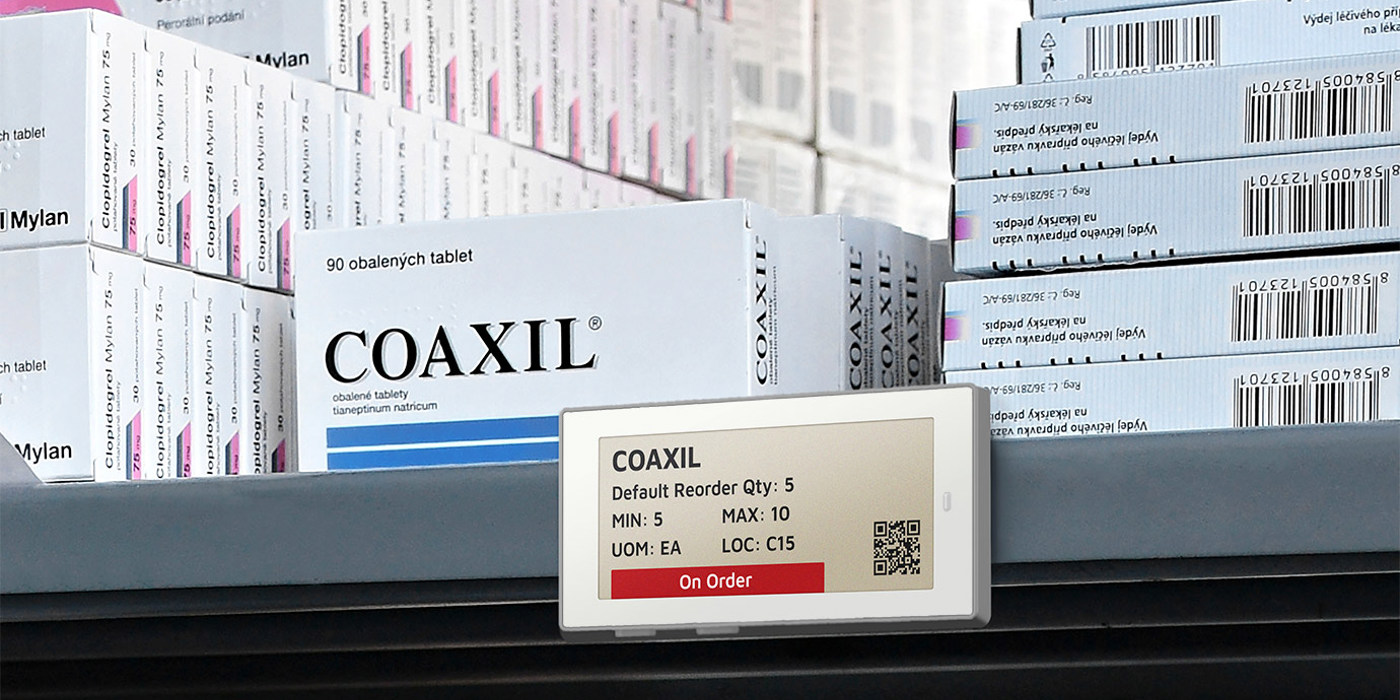
As the labor shortage rages on in the healthcare industry, many clinics and hospitals are constantly searching for ways to eliminate wasted time and improve efficiency at all levels. Inventory management tools like electronic shelf labels can help protect productivity and prevent stockouts.
Inventory Challenges In Healthcare Clinics
In many healthcare settings, inventory challenges throw a wrench in productivity and slow down operations significantly. These challenges include:
- Lack of dedicated staff to follow up on inventory needs
- Lack of reliable ordering and fulfillment systems
- Shortage of storage space for equipment and supplies
- Time-consuming counting and order creation practices
Much of the time, if an item is running low in a clinic and an order needs to be placed, the process looks something like this:
- A member of the clinical staff goes to the store room to collect an item they need.
- They notice that the item is running low or that they are taking the last one.
- They make a note to place an order, then continue with the task at hand to help their current patient.
- Now, the staff member has to remember that the item was running low, recall the correct item name and quantity left, and take time out of their day of helping patients to record this needed order on a shared whiteboard or other order request space.
- A staff member must later place the order manually, hopefully before the item completely runs out.
This process leaves too much space for human error and requires significant time and energy from clinical staff who already have enough on their plates each day. What’s more, running out of critical medical supplies can have serious consequences, especially in emergency care settings. There is a crucial need for precise inventory management and smoother restock processes.
Automated Replenishment Solutions For Healthcare Clinics
In order to streamline the task of ordering replacement inventory, healthcare teams and their distributors can implement the latest in inventory management technology.
One solution for healthcare inventory management challenges is the use of TrackStock SensorBins. These bins provide real time physical inventory counts by sensing the weight of each bin’s contents and converting that weight into item counts. This solution allows for automatic replenishment orders once inventory levels fall below the set minimum. This way, teams eliminate stockouts and save time through automatic counts and replenishment functions.
Unfortunately, many clinics and hospitals are unable to leverage SensorBin technology due to space constraints. The wide range of equipment needed in a healthcare setting means there are various item types and overwhelming space requirements. As a result, multiple different item types are often stacked in bins on top of each other when storage closets are not large enough to accommodate shelf space for every item.
For example, a team may stack three bins on top of one another, each containing a different size of sanitary gloves. From a storage standpoint, this makes perfect sense because the bins take up less space this way, but are still easy for staff to locate. However, the practice of stacking also means that SensorBins cannot be used as an inventory management solution for these items.
An additional solution to consider, especially in stockrooms with limited space, are electronic shelf labels, or eLabels. eLabels display pertinent information for the corresponding item and include a convenient button that triggers replenishment orders. This versatile solution can relieve the workload of clinical staff and eliminate the risk of stockouts.
How to Leverage Electronic Shelf Labels to Boost Efficiency
eLabels are a versatile and convenient inventory management solution. Instead of jotting down order notes on clipboards or white boards – or worse, trying to remember to place an order between patient appointments – healthcare staff can order replenishment with the push of a button. Here’s how it works:
- An eLabel is placed on the shelf storing the corresponding item. The label includes:
- The item number and name
- The default order quantity
- The min and max levels
- The item’s unit of measure
- Location information
- A QR code
- Two buttons
- When a staff member notices that the inventory on the shelf has fallen below the listed minimum, they press a button directly on the label.
- The press of the button triggers the creation of a replenishment order. This will effectively place the item into the digital shopping cart in the quantity that corresponds to the set max levels for that item.
- Multiple button presses do not create duplicate orders.
- Office staff can then manually order items from the cart from their preferred supplier, or eTurns software can place the order automatically.
This technology removes the timesuck of jotting down order notes, remembering to move inventory to online carts, tracking a physical clipboard or white board, and other small tasks that take away from healthcare providers’ time to care for patients. Instead, those providing care can focus on their work and simply press a button if they notice an item running low in their storeroom.
In addition, the QR code located on the eLabel can be scanned to input physical inventory counts in the TrackStock app whenever needed. When the accounting department needs a physical count of on-hand inventory, they can easily scan the QR code, load the app, navigate to the count module, and enter the quantity based on what they see on the shelf. eLabels boost efficiency across departments in healthcare settings.
How Electronic Shelf Labels Can Benefit Medical Distributors
In many cases, distributors working with healthcare clients can use electronic shelf labels as a value-add for their customers. Including the use of this technology means easy self-service replenishment orders from clients, as well as additional benefits on the distributor end such as:
- Fewer stockouts
- Reduction in travel time to service the customer
- Travel cost savings
- Overall reduction in the cost to serve
Without having to physically visit healthcare facilities for inventory counts, distributors can save on costs while providing excellent, convenient service.
In a field facing historic labor shortages, every opportunity for added efficiency is invaluable. eLabels from eTurns can add capacity among healthcare teams by allowing for the creation of instant replenishment orders.