5 Step to Prevent Overstocking and Understocking with eTurns’ Min/Max Tuning Slider
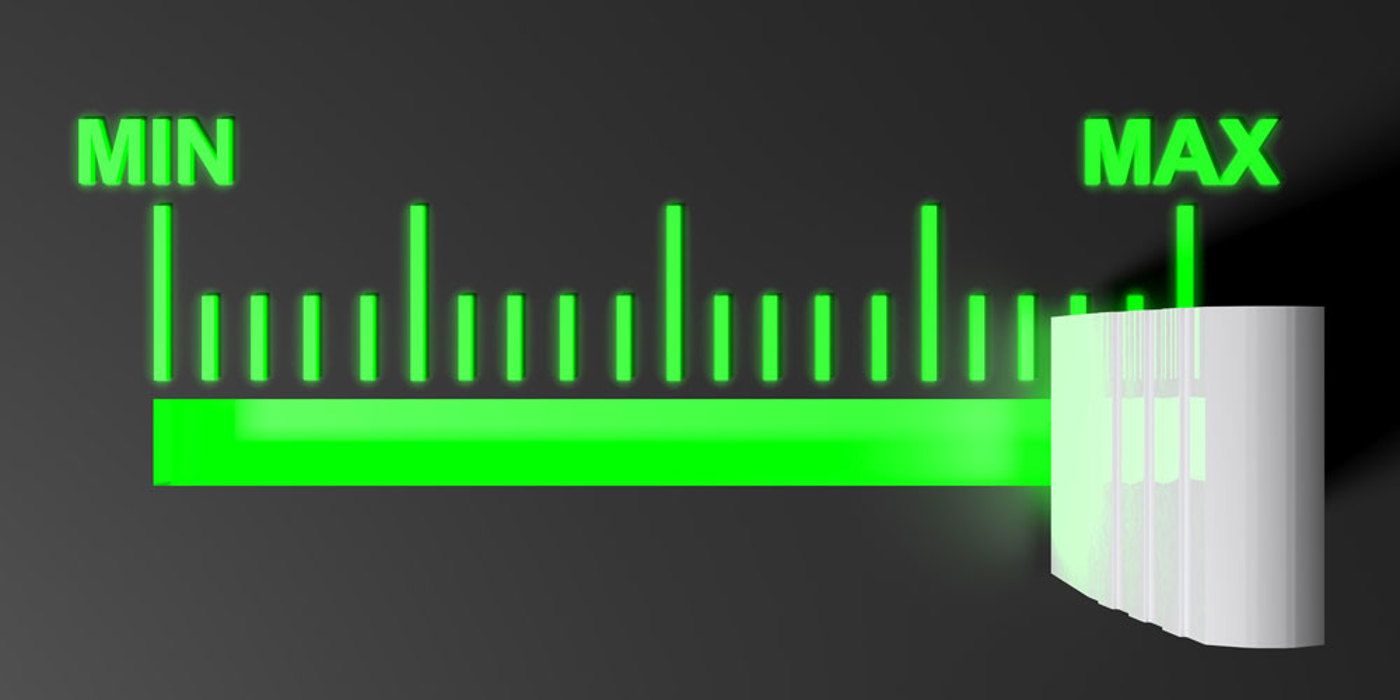
When optimizing customer inventory, distributors should use actual customer usage data and realistic scenarios that eliminate unnecessary customer expenditures on inventory and carrying costs so customers can improve profitability. That builds loyalty for sure.
One way to create those scenarios is through the eTurns TrackStock App’s Min/Max Tuning Slider, called TrackStockMMT. It’s a dashboard within the eTurns App with slider options to fine-tune on-site inventory levels by proactively calculating and suggesting optimal minimum and maximum replenishment settings — all based on data from actual customer usage.
Most importantly, TrackStockMMT calculates the cash that could be removed from the inventory on the shelves -- a HUGE opportunity to save money during these tough times on not just inventory costs but annual inventory carrying costs.
Contractors have told us that they love the eTurns TrackStock Min/Max Tuning Slider because they often have thousands of items in inventory that don’t always have a good reason for being there. When they have the hard numbers to justify trimming that inventory back, and explain why, they can move forward and confidently stock only what they need based on usage.
In this blog, we’ll review how to use the eTurns TrackStock Min/Max Tuning Slider to make sure a distributor’s customer (or a distributor doing consigned inventory) is spending as little as possible on inventory and carrying costs without stocking out.
1. First, orient yourself to the Min/Max Tuning Dashboard
The Min/Max Tuning Dashboard features boxes at the top of the screen indicating variables the user can change with just a few clicks or keystrokes. These include:
- Measurement method to calculate average daily usage: Orders or Pulls
- Days of usage to sample to calculate average daily usage
- Minimum = number of days supplier needs to replenish inventory multiplied by each item’s average daily usage over the number of days chosen above
- Maximum number of days (minimum times X number)
- Annual carrying cost as percentage of inventory value
Adjusting these variables results in an initial calculation to determine what the optimized inventory level should be.
For example, for an initial setting, you might set the measurement method to “pulls,” which refers to consumption (not orders) and adjust the days of usage (also known as days of history) to 60. This setting will add up each item’s usage over the last 60 days, then divide by 60 to calculate Average Daily Usage. You then enter the number of days your supplier needs to replenish you after they receive an order. This number of days times the average daily usage equals the calculated Minimum or Reorder Point for each item. The Maximum is a multiple of the Minimum, typically 2 – 3 times the Minimum.
2. Learn what your optimized inventory value should be and what your cash savings could be
Once you click “save,” you’ll see your “current inventory value,” then your “optimized inventory value” on the dashboard, with the cash you can save highlighted in green below that. Next, there is a calculation of the inventory value if you actually used the Mins and Maxs you have in the system today. Below that is what the cash savings are, or the cash needed to bring your inventory up to the level your current Mins and Maxs require. Finally, to the right of this group of data, is what your Annual Carrying Costs are based on your current inventory value and the percentage of inventory value you entered at the top of the screen as your Annual Carrying Costs.
3. Exploring the Slider Trial Scenario concept
On the dashboard, look for sliders below the two graphs: one for the Minimum and one for Maximum. These two graphs segment each item into one of three groups depending on how close or far away each item’s Min and Max are from the calculated Min and Max. Grab, drag and drop the slider wherever you want from 0 to 100% to indicate the percentage closer to your optimized minimums and maximums you want to move your current Mins and Maxs. TrackStock calculates what your inventory value would be using these calculated Mins and Maxs, then shows you how much cash you can save with this trial setting.
Adjusting the sliders can help create different scenarios, especially if you’d rather take small steps toward optimization than removing lots of inventory at once. For example, you can slide the minimum parameter halfway toward the optimized minimum. This is a nice option for those who are still concerned about stocking enough inventory. Try getting yourself partway there, and see how much you save. TrackStock will immediately calculate what your cash savings could be and how far off you currently are from optimized minimums and maximums.
One of the most powerful things about this tool is that you can try different scenarios and then implement the chosen scenario in realtime immediately with the “apply min/max” buttons.
4. Graphs to indicate inventory and values
The graphs on the dashboard give some context as to what the inventory levels are, as well as how many of the inventory items are within a certain percentage of the optimized level. You might find that there are hundreds of items that are currently being stocked at levels more than 50% away from optimized levels. These parameters can be adjusted by clicking the settings wheel — no spreadsheet work, no columns. Just change the numbers and hit “recalculate.”
Of course, there are exceptions to every rule. You can easily remove items from being included in the calculations if you know you always want a certain amount of one particular inventory item on hand as a spare, for example.
5. Automate for peace of mind
When you’ve adjusted minimums and maximums a few times closer to the usage-based calculated Mins and Maxs, you don't have to fuss with it manually anymore. Turn your preference to “automatic” in each item, and then, as your usage changes, it automatically changes your minimums/maximums. This determines what gets ordered and when, and can give you greater peace of mind.
Learn more about the Min/Max Tuning Slider by requesting a demo today.