Kanban Inventory Control: How IoT SensorBins Improve On This Traditional Method
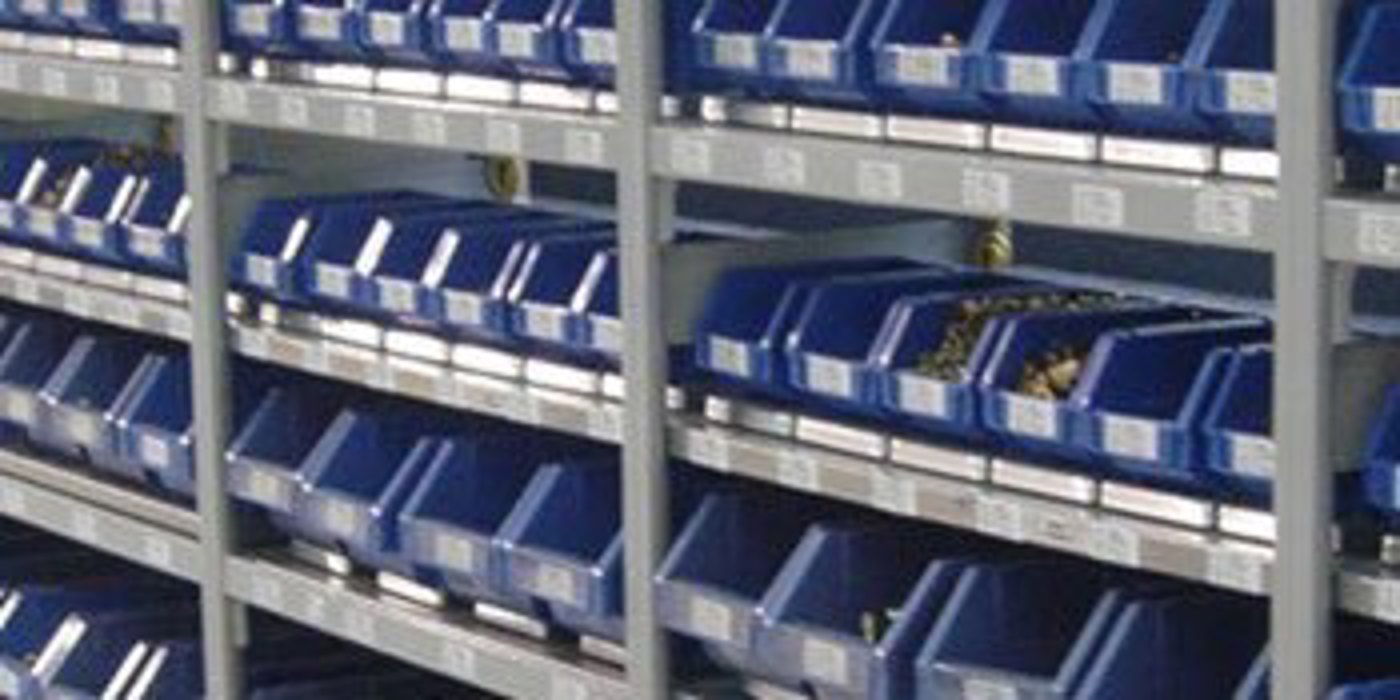
If you’re a stockroom manager, you know how the past two years have affected your job. With containers full of supplies waiting to be unloaded at the docks, and a labor shortage, it’s become increasingly difficult to reliably track and replenish stockroom inventory.
Traditional processes that worked when times were steadier no longer fit the bill. It’s more important than ever to have a stockroom inventory management system that provides real-time data based on actual usage rather than historical data. Organizations such as manufacturers and medical clinics need to keep on top of vagaries in the supply chain, all while dealing with a shortage of reliable, skilled help and need every innovative tool at their disposal.
To track inventory and ensure timely replenishment, stockroom and operations managers have long relied on traditional methods like the kanban system for inventory management to track usage and know when to replenish supplies. And while kanban has been a successful method in the past, new technologies such as SensorBins , IoT weight sensors that pair with the eTurns TrackStock automated inventory replenishment app, have revolutionized the inventory replenishment task for stockroom managers.
Like kanban, eTurns TrackStock SensorBins, is an inventory management system that relies on real-time point-of-use inventory consumption (usage) to trigger replenishment (supply). And while both methods serve the goal of ensuring you never run out of items and don’t stock too much, Kanban stops there and eTurns TrackStock SensorBins has additional compelling benefits for optimized stockroom replenishment.
Kanban Method Principles
First, let’s review Kanban. Many stockrooms use a kanban system to track stock usage and replenish inventory. Kanban is a Lean methodology, a visual system developed by an industrial engineer at Toyota to manage production flow. The goal when used with inventory management is to have the minimum amount of stock on hand necessary at the time. This allows organizations to purchase only what is needed and not carry excess inventory.
The kanban system is known as a pull system because production is pulled through the workplace by customer demand. Kanban inventory management works by a card system to signal when a particular action should occur – in the case of a stockroom, when inventory needs to be reordered. As inventory is consumed, kanban cards are used to determine when the item needs replenished. Typically, a two-bin solution is used in stock and supply rooms. It works by placing two bins of a specific item on a shelf, one in front of or next to the other.
When the first bin is emptied, it is removed and the second bin is moved in its place. The kanban card from the empty bin is manually scanned or placed on a kanban board for tracking and reordering.
A kanban card is a signal to order material and usually includes basic information about the item and its kanban solution: part number, description, order quantity, standard pack quantity, supplier, lead time and storage location and relies on a dependable staff to move the card to the proper location for replenishment.
Automated Replenishment with eTurns SensorBins
Instead of relying on a card solution, eTurns TrackStock SensorBins™ automate the monitoring of inventory levels and optimize the replenishment. eTurns SensorBins utilize weight sensors that can be placed under bins, on a stockroom shelf, on mobile racks and in jobsite containers to bring the supplies close to where they are needed.
SensorBins™ are a no-touch solution. The weight sensors work together with the eTurns TrackStock app for fully automated tracking and replenishment. SensorBins convert bin weights to quantity to allow complete physical inventory counts multiple times a day without human intervention, and then automatically reorder if the quantity is less than the minimum set level.
In an environment where inventory items are either critical or used at a fast pace, the ability to track inventory in real time is vital.
Industries that have high inventory turnover rely on suppliers to offer vendor-managed inventory (VMI) services to ensure critical inventory is always in stock. In a VMI system in a manufacturing environment, for example, the supplier typically tracks and manages the inventory located in the manufacturer’s stockroom for them, but the inventory is rarely optimized. Having a system like eTurns SensorBins allows the supplier and their customer to automate and optimize the replenishment of inventory with accurate consumption data at their fingertips.
IoT Inventory Management: How to save money with eTurns SensorBins vs Kanban
There are many advantages of using eTurns SensorBins over a kanban system, including:
Save Stockroom Space -
There’s no need to have extra bins of backup stock with eTurns; just one bin with a weight sensor is needed. A kanban two-bin system would take up double the stockroom shelf space of the eTurns SensorBins solution. This is especially helpful when stocking large items. In fact, the eTurns SensorBins solution provides flexibility in stockroom organization because they can be configured to measure the weight of an individual bin, an entire shelf, bench, cart or pallet. This reduces the size of the stockroom and saves stockroom staff time in duplicating bins, while allocating more space to production.
Optimize Replenishment to Save Money on Inventory and Carrying Costs -
Since there’s no need to have a second bin of every item in your stockroom, you can enjoy one-time savings in immediately stocking fewer items, and you get on-going savings by not having the carrying costs of owning double the inventory year after year. And the Min/Max Tuning Dashboard in eTurns ensures that your one bin of items is only replenished to optimized levels.
Eliminate Errors From Manual Card Work -
Your staff won’t have to move the cards or scan the cards for orders because with eTurns SensorBins, the items are tracked as they are consumed, from any location around the world, and orders are automatically triggered when minimums are breached. And with eTurns SensorBins, there’s no dealing with misplaced or duplicated cards, eliminating errors and saving money.
Notice Flunctuation in Usage Earlier -
The kanban system doesn’t work as well when dealing with fluctuations in demand or products. It works by assuming a stable, repetitive production cycle where the supplier delivers items when needed. Because eTurns SensorBins continually measure item usage, any fluctuation in demand is noticed right away. And the eTurns Min/Max Tuning Dashboard offers options to fine-tune on-site inventory levels by proactively calculating and suggesting optimal minimum and maximum replenishment settings — all based on data from actual customer usage.
Reallocate Labor to More Useful Tasks -
The kanban system depends on staff moving bins and cards and operating by the rules of the process. If the rules are forgotten or ignored by employees, the replenishment process breaks down. And if you’re dealing with a labor shortage, using staff to manually track and manage inventory with kanban is a waste of skilled labor that can be reallocated elsewhere. With eTurns SensorBins, there’s no need to train employees or rely on them to move cards, or worry that the cards reached the person in charge of contacting the supplier because it’s all automatically done, including triggering the replenishment order.
Using an automated stockroom inventory management process with eTurns SensorBins technology not only saves your company time and money, it alleviates the headaches of many stockroom managers. When an employee calls in sick or walks off the job, the stockroom manager knows that with eTurns, the vital inventory needed to keep their operation going will continue to be tracked and replenished. And isn’t that what you need in today’s unpredictable market?