How to Calculate Optimal Inventory in Stockrooms and DCs
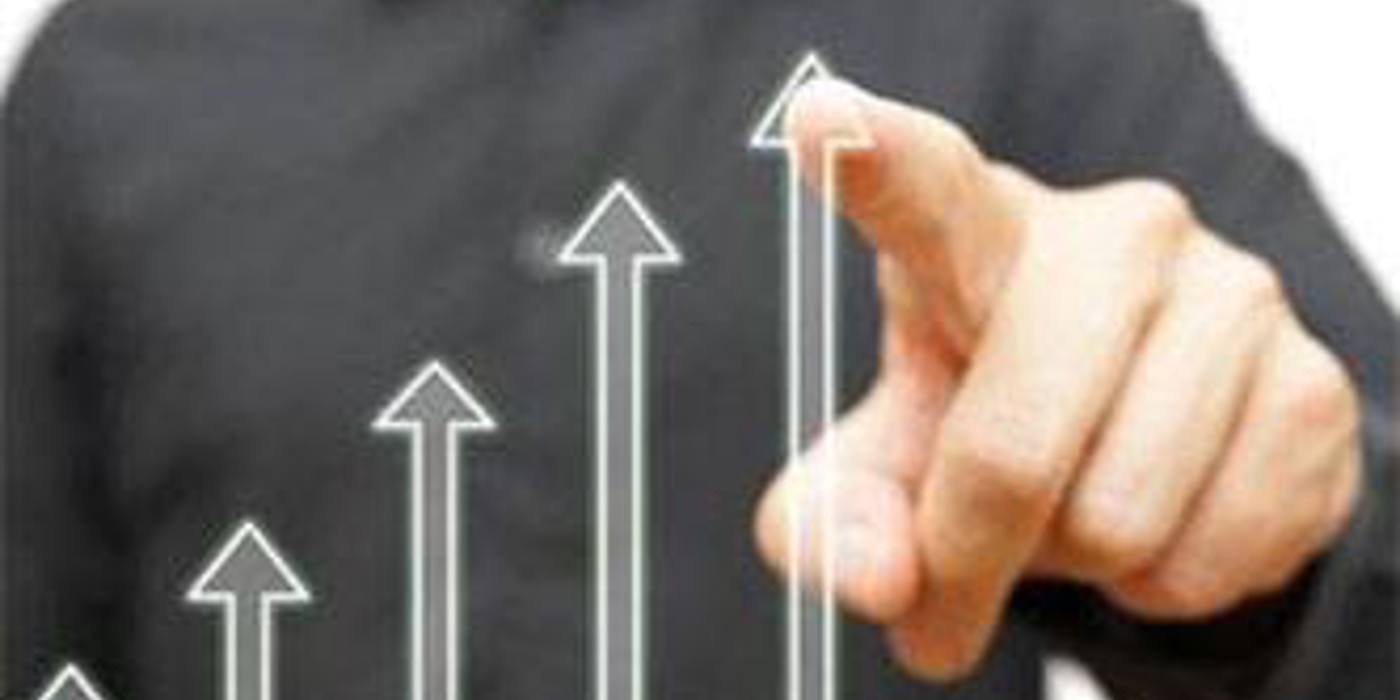
One of the hardest tasks for distributors and their customers is to optimize the customers’ inventory levels, ensuring enough quantity on hand for their purposes, but avoiding excess inventory so they don’t incur additional carrying costs.
There are all sorts of ERP solutions that track inventory in a distributor’s warehouse, but only a few automated replenishment apps help manage and optimize the inventory that sits downstream in an end-customer’s stockroom.
And this is where both the pain and the opportunity lie.
By optimizing these customer stockrooms there is the potential to:
1) ensure no stockouts
2) remove cash from shelves by decreasing inventory levels
3) decrease yearly recurring costs by lowering inventory carrying costs
4) save time by replenishing with barcode scans or weight sensors
What is inventory optimization?
Most companies simply guess at how much inventory they need to stock in order to have the right item at the right time in the right quantity. Many companies hold excess inventory to prevent stockouts. This buffer compensates for potential variations in supply, as well as vagaries in the information they are receiving about current demand, forecast demand and uncertain lead times.
Companies must say goodbye to the buffer as an effective strategy.
The only way an organization can accurately calculate what they need to replenish inventory while keeping optimized inventory levels is by tracking actual inventory usage – and that’s impossible to do without the right technology, such as the eTurns TrackStock app. eTurns TrackStock increases inventory visibility, optimizes inventory, and lowers procurement costs in stockrooms and service trucks.
How to calculate optimal inventory level in customer stockrooms
1. Obtain actual inventory usage data with the eTurns TrackStock app for at least 45 days, when eTurns can then calculate and suggest optimal minimum and maximum stocking levels for each item based on actual usage and current lead times.
2. Use eTurns Min/Max Tuning Dashboard to reset your current Min/Max levels to the suggested optimal levels so that future orders are optimized. Instead of relying on manual inventory tracking, the eTurns TrackStock cloud app records the customer’s actual usage via phones, scanners, RFID or our most sophisticated and automated method, IoT SensorBins.
For distributors that are not allowed to access their customers’ stockrooms or must travel to remote places to do inventory counts, the eTurns SensorBins IoT weight sensor solution is ideal for inventory optimization. Weight sensors under bins of supplies work with the eTurns TrackStock app for fully automated replenishment. Distributor Gexpro Services implemented the solution at a large powergen manufacturer in Ohio, reducing stock by nearly $1 million, while providing access to real-time on-hand inventory data.
How to calculate optimal inventory levels in distribution centers and eliminate forecast errors
eTurns TrackStock Precise Demand Planning eliminates forecast error for distributors by calculating demand based on what customers are using, not what they have historically ordered, which is a huge benefit in this era of turbulent supply chains.
If distributors use eTurns TrackStock to automate replenishment of their biggest customers’ stockrooms, eTurns can provide those usage analytics to distributors so that distributors can optimize the demand forecast in their distribution centers and eliminate forecast error. Often we find that distributors get 85% of their revenue from only around 7% of their customers. So if those 7% use eTurns for managing customer stockroom inventories, the distributor will always have accurate usage and demand data to feed into the demand planning process for their distribution centers.
eTurns knows precisely when each customer will order what product on what date in what quantity
So distributors get a win-win. First, they have happy, loyal customers because they've given the customers an app that optimizes replenishment of point-of-use inventory in customer stockrooms.
Second, distributors can collect customer usage data (about who will buy what product on what date in what quantity based on the trends of the past 45 days of usage, plus known min/max levels, requisitions, etc.) that, when aggregated, allows the distributor to fine tune the demand requirements in their distribution centers and eliminate forecast errors.
Read more about eTurns TrackStock Precise Demand Planning.
For more information on how eTurns TrackStock mobile inventory app increases inventory visibility, optimizes inventory, and lowers procurement costs in stockrooms and service trucks, reach out to us or try eTurns free for 30 days, including set up and great phone & email support.