The Benefits of Min/Max Inventory Management
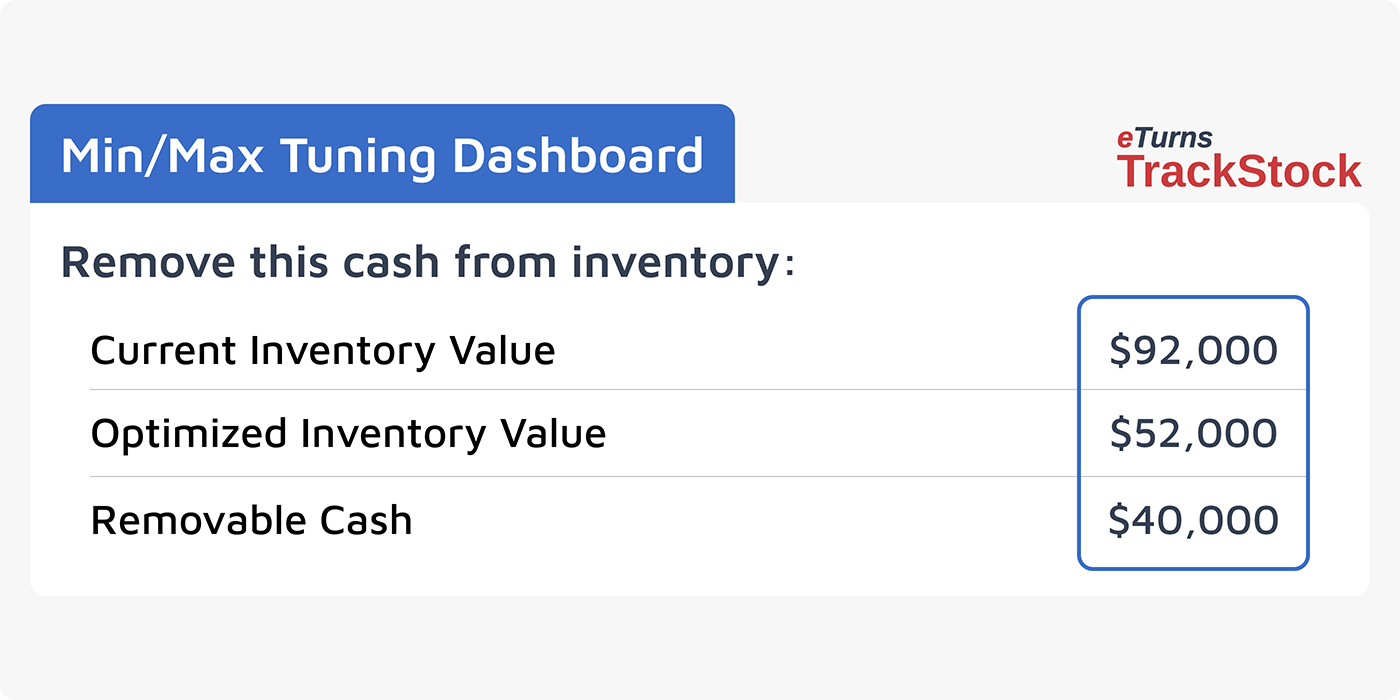
What is Min/Max Inventory Management?
Min/max inventory management is the process of designating minimum and maximum levels for each of your products and reordering stock whenever the minimum level is reached. This is a common approach in modern inventory management and reduces the likelihood of under or overspending.
The best way to ensure your consumable inventory or MRO inventory is optimized is by using the min/max technique. Fundamentally, the min/max method keeps current on-hand inventory within a specific range with a high degree of accuracy.
First, you set a minimum (min) stocking level, which--when reached--triggers a reorder to reach the maximum stocking level of that item. Second, the maximum (max) level prevents your reordering automation from overstocking and therefore overspending.
How Do I Manage Consumable Inventory Easily with Min/Maxes?
To manage consumable MRO, industrial, or medical inventory using optimized min/maxes that trigger auto-replenishment, you need to do these steps:
- Select a min/max inventory management app that can track inventory at the point-of-use.
- Decide what method of inventory management you want to use:
- Cycle Counts / Inventory Audits
- Pulls from Consigned or Customer-owned inventory
- Orders
- Vendor-managed inventory (VMI) or customer-managed inventory (CMI)
- Decide what technology you want to use with the app to capture usage:
- QR code scanning app
- SensorBins weight sensors under bins of material
- RFID
- Upload your items/user/supplier/product info to the app and set initial min/max settings.
- Use the app to track your usage.
- Let the app calculate your optimized min/max settings and available savings if you move to optimized min/maxes.
How Do I Calculate Min/Max Levels with a Min/Max Formula?
The min/max reordering formula is straightforward: it's the difference between the maximum and the quantity on hand minus what is already on order or on requisition.
This is what it looks like:
Maximum Formula: Maximum (MAX) - Quantity on hand (QOH) - On Order = Quantity to Order
Note: If you're operating from a business with demand uncertainty, supplier uncertainty, and lead time uncertainty, consider the following min/max formula for calculating your minimum:
Minimum Formula: Safety Stock + (Daily Run Rate x Lead Time) = Minimum (MIN)
However, the only way to set accurate min and max levels that will prevent stockouts and help optimize inventory levels is to calculate average daily usage. Modern inventory replenishment apps need about 45 days of tracking consumption and lead time inputs to suggest initial min/max levels that can be dynamically and automatically adjusted to optimize inventory.
Over time, your min/max levels need to be tuned and optimized with a larger volume of usage data. This approach further optimizes inventory levels to keep costs low and profit high.
How Does Min/Max Inventory Management Really Work?
Determining the levels at which to set your min and max at depends on the answers to several questions. How quickly can your suppliers fulfill orders after you place one? Is the demand for some items greater in the next 30 days than 120 days from now? Which items need spares so that they never fall below two on hand?
All of these questions must be answered to optimize your inventory’s min/max in the midst of external factors like seasonality, supplier reliability, and team consistency. Consult experts on your team to address any gaps in your thinking before setting your levels, then implement it to achieve cost savings as soon as possible.
A skilled job supervisor or an experienced tech can set useful approximate starting points for your minimums and maximums for any item. These levels can be manually reset as time passes and your techs watch the inventory levels as they use parts.
However, there's a breakdown of communication and consistency on teams doing manual replenishment. As a result, the minimums and maximums are not adequately adjusted over time. Then, stock levels do not match usage needs at the point-of-use stockroom.
Too much of some items and too little of others results in wasted time and money from stockouts and overstock.
Manually tracking item usage and adjusting min/max settings ends up being wasteful.
To overcome this problem, you need an app that can track usage automatically and adjust min/max settings dynamically. Without an app that tracks consumption of material on the job, you won't realize the true potential of min/max inventory management. You need the ability to “tune” those min/maxes dynamically based on item usage to optimize inventories and maximize service levels.
Said differently, we want to reduce inventory levels to the absolute minimum to save cash while making sure we do not stock out of any item to keep the job moving.
Who Uses Min/Max Levels For Inventory Management?
All industries that maintain inventory at the point of use strive for the same strategic objective:
Reducing inventory to the absolute minimum without stocking out. ✅
The following industries all benefit from deploying min/maxes to optimize their inventory:
- Healthcare for their clinics and hospital supply rooms.
- Manufacturers for their long-tail maintenance, repair, and operations (MRO) consumable inventory.
- Contractors on their job sites.
- Distributors when they consign inventories .
- Mining companies so they don’t require rush restocking.
- State governments to keep the correct amount of items to support their tourist traffic.
- The service truck industry to properly stock their trucks to prevent unneeded trips to a supplier to restock items for service calls.
- Every business that uses Amazon or other suppliers to restock their indirect needs of office supplies, janitorial supplies, IT supplies, medical supplies, and breakroom supplies.
The overall strategic objective is to optimize inventories and maximize service levels. These industries need an app that tracks consumption at the point-of-use and uses it to their strategic advantage.
How Do I Set Min/Max Levels Accurately for Optimized Stockroom Inventory?
Having accurate min/max levels that help you maintain optimized inventory in your stockrooms is dependent on your ability to track the usage of each inventory item over a recent period of time.
In addition, you need to account for these variables:
- Supplier lead time
- Inventory turns for fast-moving items
- Different categories of items, such as spares and unique items
Average daily usage over the past 45 days is a great starting point for setting min/max levels, but they'll also need to be constantly adjusted. One of the largest challenges in setting levels without the use of a tracking app is the manual effort required to derive this very useful statistic: average daily usage.
As soon as you calculate that number, how long would it take to determine what the average daily usage is for 80 days or 120 days? It requires more hours than anyone has available. This is why, historically, stockroom optimization analysis attempts are conducted at most once a year. Businesses need an app that can perform this calculation in three seconds so you and your team can spend your brain power on progressing to optimized min/maxes.
"TrackStock’s Min/Max AI Dashboard shows you how much money you can save in one-time inventory reduction as well as annual carrying costs by moving to optimized min/max levels."
How the TrackStock Min/Max AI Dashboard Dynamically Adjusts Your Levels Based On Actual Usage to Optimize Stockroom Inventory
eTurns TrackStock is a mobile app for self-service customer-managed inventory (CMI) or vendor-managed inventory (VMI). You scan the barcodes of items that are being removed from inventory and used. It tracks consumption. By storing this item usage data, in addition to the following important variables about your suppliers and your organization, our app calculates optimal min/max levels for each product.
For instance, the app factors in lead time. Users need to evaluate their distributor or supplier’s performance on delivery time from order to receipt.
If this period is two days, then perhaps the minimum levels should be set to four days of average daily usage to be conservative. This provides some buffer time for the typical item. TrackStock lets you filter specific items that have longer lead times in order to calculate what their minimums should be in comparison to typical items.
TrackStock also factors in supplier details. For instance, once users have an idea of what the minimums should be, they need to decide at what levels the maximums should be set. Are they twice the minimums? 2.3 times? 3.7 times?
Again, it's dependent on a number of variables such as distributor or supplier performance, physical distance from the supplier, inventory turns, perishability, and more. TrackStock keeps track of all of these variables and calculates the optimized min/maxes.
TrackStock offers a min/max tuning slider for users who aren’t ready to immediately trust the automatically-calculated optimal min/max levels. Once TrackStock calculates optimal min/maxes, the user can use the slider bar in the Min/Max Tuning Dashboard to gradually and conservatively move the current min/maxes toward the optimal ones. TrackStock allows the user to reset all of the min/maxes from the Min/Max Tuning Dashboard rather than entering each one manually.
After running with these new min/maxes for a month or two, the user can use TrackStock’s Min/Max Tuning Dashboard to recalculate what the min/maxes should be based on the most recent usage. You can then use the slider again to move the current min/maxes closer to the optimized min/maxes, then set all the levels from the Dashboard again.
When you're close to the optimized min/maxes, you can set the app to calculate the optimized min/maxes for each item and reset them automatically after each “Usage Pull” or after 24 hours if there were no Pulls. Either action will change the average daily usage since another day without a Pull will reduce the average. This responsive system allows for heightened accuracy and more efficiency.
"To be honest, most of the customers we have surveyed are stocking 50+% more inventory than they need and they are amazed when TrackStock shows them exactly how much they could save in a one-time inventory reduction and annual carrying costs, based on the past several weeks or months of recorded usage with our TrackStock app."
What Are the Financial Benefits of Setting Optimal Min/Max Levels With TrackStock?
Our Min/Max AI Dashboard calculates and displays exactly how much money you can save in one-time inventory reduction as well as in annual carrying costs by moving to optimized min/max levels.
To be honest, most of the customers we have surveyed are stocking 50+% more inventory than they need and they are amazed when TrackStock shows them exactly how much they could save in a one-time inventory reduction, based on the past several weeks or months of recorded usage. Our customers have been able to reduce inventory levels up to 73% with optimization.
Overstocking inventory means not only spending too much on the inventory, but spending too much on carrying costs as well. Carrying costs include: supply room expenses, hourly and salaried labor, taxes, insurance, obsolescence, theft/shrinkage, and clerical costs. Carrying cost industry averages range from 25% to 55% of inventory value.
Once the carrying cost percentage for the business has been determined, TrackStock adds it to the data it has on your average daily usage and your procurement variables. Then, TrackStock lists in the Min/Max AI Dashboard the actual cash savings available from a one-time reduction of your business's inventory, as well as the annual cash savings from reduced carrying costs.
Case Study: Service Trucks
One service contractor, Service America, reaped the following benefits in the first year using the eTurns TrackStock app.
Here are the results they got:
- Inventory accuracy improved by more than 45%
- Truck inventory levels decreased by over 30%
- Warehouse inventory decreased by over 45%
What Min/Max Reports Does eTurns TrackStock Offer?
In addition to calculating the optimized min/maxes, TrackStock also provides an incredible array of statistics and reports for each item.
These can be sent in email alerts on a schedule and they include:
- Total pull quantity, pull value, and order usage for the period.
- The average daily value for each of the above.
- What quantity of the item will be consumed before the next order.
- How many days until the next order and the date of that order.
- How much will be ordered.
- Annual inventory turns using pulls and orders.
"TrackStock allows the user to reset all of the min/maxes from the Min/Max AI Dashboard rather than entering each one manually."
Ready to Try eTurns TrackStock?
Schedule a demo or start your free trial and see how easy it is to use eTurns to set min/maxes for your storeroom inventory.