Carrying Costs of Inventory: What It Is & How to Calculate It
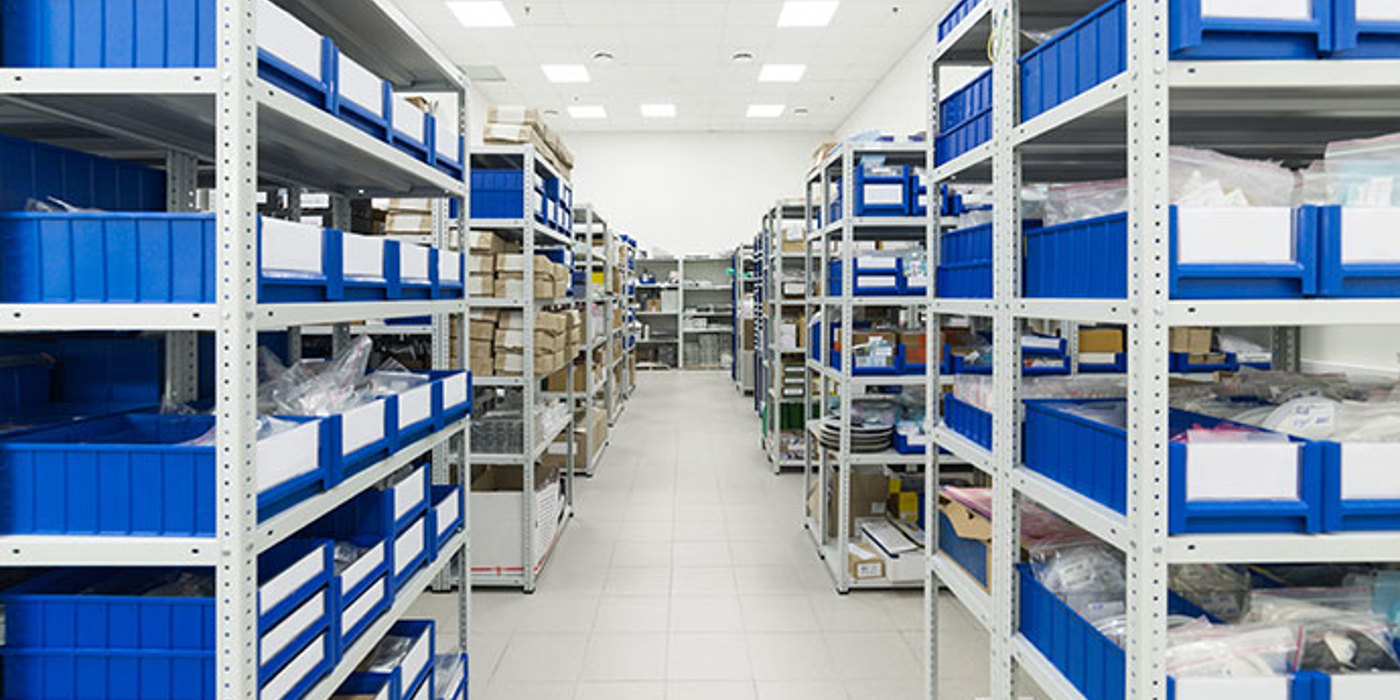
Gaining a deeper understanding of your carrying costs of inventory can increase profits overall, but the task is easier said than done. Determining your company’s overall carrying cost of inventory can help you understand how much you have to gain by optimizing inventory levels and only paying to carry the inventory you absolutely need. Tools like eTurns TrackStock can help you optimize replenishment and minimize your spending on inventory and carrying costs. Free up cash while reducing stockouts.
What Is Meant by Carrying Cost of Inventory?
Carrying cost refers to the amount of money spent to hold inventory over a given period of time. While this concept may seem one-dimensional at first glance, there are various factors that play a role in determining the carrying cost of different inventory items. All expenses tied to storing, owning, stocking, and handling the inventory are part of the carrying cost, in addition to other expenses such as taxes, insurance, shrinkage, depreciation, and even opportunity costs.
Because there are so many factors that play a role in carrying cost and because usage cycles can change quickly or unexpectedly, calculating and thoroughly understanding inventory carrying cost is particularly nuanced. For this reason, carrying costs continue to pose one of the largest inventory management challenges of all.
Understanding Inventory Carrying Cost
Understanding the carrying cost of your inventory is crucial for determining how much money you could be wasting by holding unneeded inventory. In many cases, inventory is both the largest asset and the largest expense of a business. The overall goal is to reduce carrying costs without risking stockouts, which can be a tricky equation to nail down alone. Striking this balance is the best way to increase profitability with better inventory management.
Carrying costs are generally shown as a percentage of the total inventory value. As a rule of thumb, a business’s carrying costs usually add up to approximately 25-55% of the value of the inventory overall. This number will vary based on the type and size of the business. Thoroughly understanding your inventory carrying costs is crucial as they directly impact future cash flows and the cost of capital for the company.
Some aspects of inventory carrying costs are easy to understand and quantify, such as the cost to store items, the labor required to handle them, and the taxes and insurance on the goods. On the other hand, some inventory carrying costs are not as easy to put a number on. For example, an important aspect to integrate into a carrying cost equation is opportunity cost. This refers to the fact that overspending on inventory takes away money you could have used for other capital-generating activities, such as marketing or investment opportunities.
Another aspect of inventory carrying cost that isn’t so easy to predict is depreciation. Some stock loses its value over time and can even become obsolete and impossible to sell at the end of its lifecycle. Depreciation increases carrying costs, and obsolescence causes a sharp spike as the items become impossible to sell at all. In some cases, companies can plan ahead to offload stock before it loses all of its value through discounts, donations, or liquidation.
What Are Examples of Inventory Carrying Costs?
To better contextualize inventory carrying costs, it’s helpful to consider an example.
A plumber keeps inventory including pipes, tape, glues, etc. The plumber has an annual inventory value of $25K. They spent $5K on transporting the stock, storing what won’t fit on the shelves, paying employees to shelve and maintain the items, and more. Some of the stock isn’t used before it expires, leading to $2K in obsolescence. These costs add up to $7K out of the total $25K inventory value, leaving carrying costs at 28%.
How Do I Calculate Inventory Carrying Cost?
Due to the overwhelming number of factors that work into inventory carrying costs as a whole, calculating inventory carrying cost can be tricky. Every business is different, and some costs apply to one company type but not to others.
The first step is to determine which carrying cost components apply to your business. For example, what do you pay for storage? For transport? Add in components like inventory service cost and inventory risk cost if applicable. Add each of these together to calculate your carrying cost total. Then, to calculate your percentage, divide that total by the total value of your inventory.
Once you know your approximate carrying cost percentage, plug it into the eTurns Inventory Management ROI Calculator to understand how much you could save on carrying costs by using an auto-replenishment app to optimize inventory levels. Reducing carrying costs is one of the best ways to increase profits, but doing so accurately without the proper tools and calculations is next to impossible.
eTurns TrackStock cloud software allows businesses to easily count inventory, optimize inventory levels with analytics, and automatically replenish stock when needed.