No-Touch Medical Inventory Management? It’s Possible with IoT Sensors
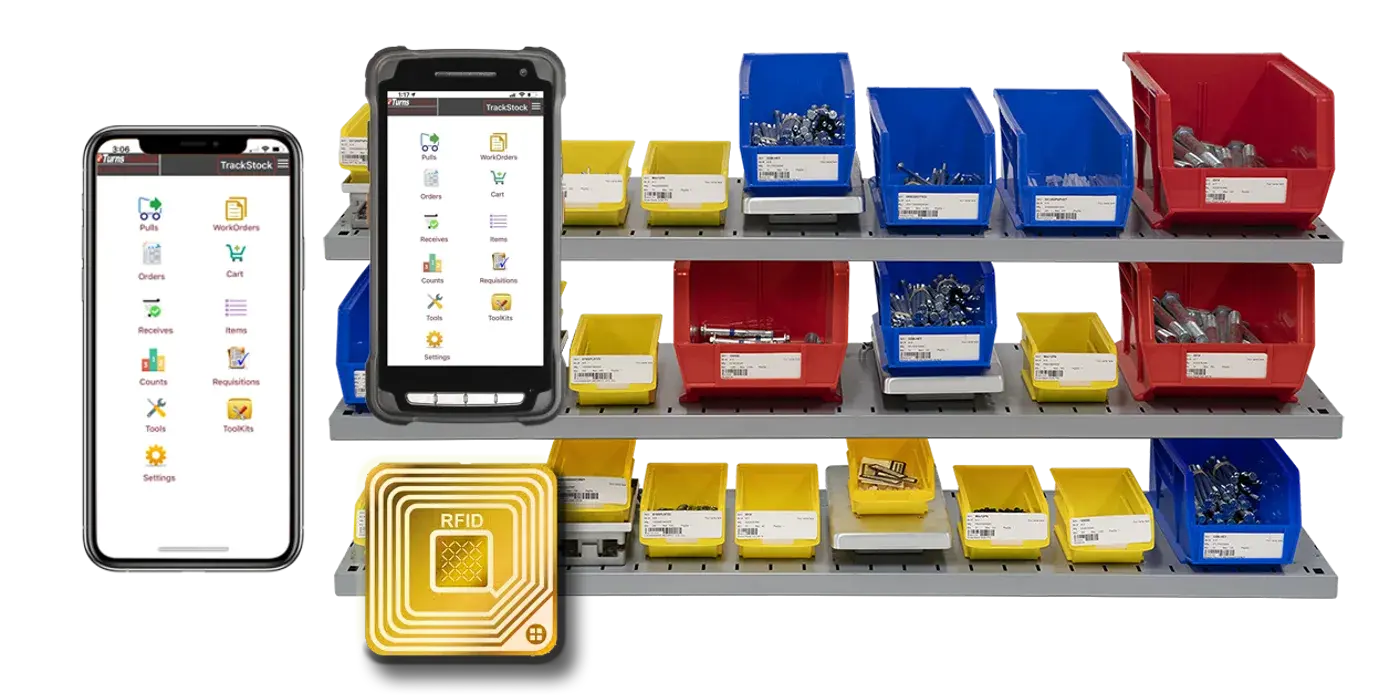
Over the past few months, we’ve seen increased interest by medical clinics, EMS organizations and healthcare facilities in our Internet of Things-based automated inventory management and replenishment apps, which require little human intervention.
The Internet of Things (IoT), the foundation of our eTurns SensorBins solution, has come of age and is being used in everything from sensor-based preventive maintenance in manufacturing facilities to smart thermostats and security systems in consumers’ homes.
The use of sensors for inventory management drives efficiency, prevents stockouts and, of course, enables social distancing. In fact, SensorBins remove the need for humans to monitor inventory levels at all.
The demand among medical and healthcare organizations makes sense. Supply chains are broken due in large part to global sourcing (long lead times and little control), and companies are unable to scale up quickly in times of crisis. We saw this when medical workers couldn’t get masks, testing kits and related critical supplies, as well as ventilators to keep themselves and their patients safe.
In addition to mitigating the unpredictability of the supply chain, medical clinics and healthcare facilities want to limit the number of people required to manage inventory in-house and want to keep supplier reps out as much as possible to limit exposure.
How can we rebuild the integrity of the supply chain, focusing first on the start of the demand chain (point of use) while providing automated replenishment without spreading of disease? One way to reduce volatility is to automate inventory management.
Inventory replenishment with little human intervention is possible with the use of IOT sensor-based inventory management, or eTurns SensorBins.
How eTurns SensorBins Works
The eTurns SensorBins solution puts an Internet of Things weight sensor under a bin of material (between .012 ounces and 3,200 pounds) on a stationary rack or mobile rack. The sensor then monitors current on-hand quantity by measuring the weight of the parts on it at user-defined intervals.
When the weight falls below a minimum, a replenishment order up to the maximum is sent via the eVMI cloud-based application to a distributor’s ERP system. That means a supplier does not have to visit the location to manually assess whether inventory is required; eVMI converts bin weights to quantity and can do a complete physical inventory count before the supplier makes a replenishment run or fulfills the order and ships the supplies. The customer then restocks the bins.
The benefits of this hands-off approach include:
- Provides real-time tracking of inventory on-hand quantities without human intervention.
- Eliminates stockouts with 24/7/365 visibility and automates reorders when inventory falls below a minimum level.
- Optimizes inventory with analytics that adjust min/max levels.
- Removes human error.
- Reduces up to 90% of procurement costs.
- Reduces inventory levels and annual carrying costs by up to 73%.
- Increases efficiency.
Want a demo of eTurns SensorBins or eLabels? Happy to show you. Please click here.