ABC Analysis in Medical Inventory Management: 3 Key Considerations
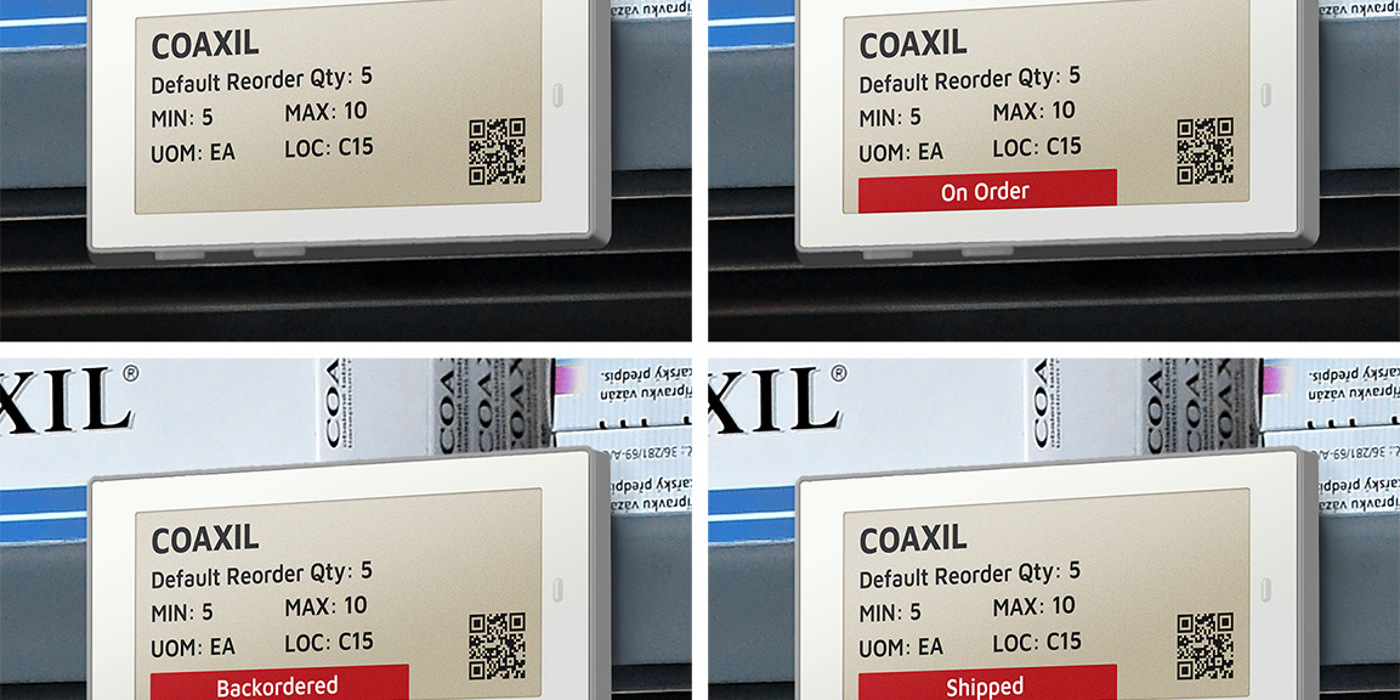
- What is ABC Analysis?
- How Does ABC Analysis of Inventory Work?
- Benefits of ABC Analysis in the Medical Field
- How to Apply ABC Analysis in Clinics and Medical Institutions
Managing inventory in the medical field requires a robust system that delivers precision, speed, and cost-efficiency at every turn. Having properly tracked and readily available inventory is truly a matter of life and death in this field, calling for accuracy and reliability from the inventory management system. In the effort to strike the delicate balance between keeping inventory optimized and using resources and labor efficiently, many medical institutions utilize an ABC analysis model of inventory management.
What Is ABC Analysis?
ABC analysis is an inventory management method that categorizes items based on priority, value, and relative importance to the institution. In doing so, this method takes into account the overall costs associated with closely tracking and controlling inventory. Instead of making a stringent effort to precisely monitor every single item, ABC analysis of inventory leverages categories to determine which items require the most attention. This ranking system takes demand, cost, and risk into account in order to classify every inventory item into one of the following buckets:
- Class A: These are the most valuable or important items. The Pareto principle, or 80/20 rule, suggests that a large portion of an organization's value (about 80%) comes from a small portion (about 20%) of their inventory. Using this principle, many organizations designate about 20% of their highest-value inventory as A-class items. These items require rigorous monitoring and management due to their critical importance.
- Class B: These items are of moderate value and importance. They require a balanced level of attention and resources.
- Class C: These items have the lowest value and often constitute a majority of the inventory. While they may not individually impact the bottom line significantly, as a whole they still play a role in day-to-day operations.
The analysis ABC classification system helps inventory management teams to divide their attention appropriately, spending the most time and effort on managing the Class A items and the least on Class C items.
How Does ABC Analysis of Inventory Work?
In order to implement an ABC analysis inventory management approach, medical institutions must leverage available data to appropriately categorize each item. Laying the groundwork for ABC analysis in medical inventory management generally involves the following three steps:
1. Data collection: Gather data on the cost, usage, and importance of each item in the inventory. Precise medical inventory tracking software such as eTurns TrackStock can help medical institutions easily identify which items are most heavily used and which carry the highest value.
2. Ranking: Sort items based on the annual usage value per product in order to determine their ranking. Calculate the annual usage value per product using the following equation:
Annual usage value = (Annual number of items sold/used) x (Cost per item)
In a medical setting, critical items would also assume a higher ranking.
3. Categorization: Assign specific criteria for each category, such as percentages of total inventory value. For example, A items might constitute the 20% of items that account for 80% of the total value. B items might include the 30% of items that account for 15% of the total value. C items would be the 50% of items that make up 5% of the total value.
Once each item has been categorized, teams can work up category-specific action plans that promote labor and cost efficiency while protecting valuable assets.
Benefits of ABC Analysis in the Medical Field
Constraints on space, labor hours, and money force medical professionals to adopt lean practices for inventory management. There’s no extra time for double and triple checking every count of the lowest-value items. There are also dire consequences for stockouts of lifesaving supplies. As such, a strategic approach to inventory management is a must in hospitals, health clinics, and other medical institutions. These three key benefits make ABC analysis a sound practice.
- Prioritize inventory: In a medical setting, ABC analysis enables precise allocation of attention and resources. Vital medical supplies, medications, and equipment can be closely managed to prevent disruptions in patient care, without any unnecessary burden on healthcare labor.
- Identify critical items and avoid stockouts: By focusing the majority of their time and resources on class A items, healthcare institutions can mitigate the risk of stockouts for crucial supplies.
- Cost savings and efficient resource allocation: ABC analysis helps optimize labor and resource allocation. High-value items can be closely monitored to prevent stockouts or overstocking and running out of storage. Low-value items can be managed with a more lenient approach, reducing unnecessary time constraints and costs.
Overall, the ABC analysis of inventory helps balance appropriate inventory levels of high-value and critical items with the need to keep operations lean and efficient.
Since eTurns gives me a report on the cost of supply utilization for each surgical day plus total usage per month, I am able to keep a pulse on our net surgical profit consistently and without burning up too much of my time. It is great to track all procedure material costs and our real-time inventory status.
How To Apply ABC Analysis in Medical Institutions
In order to implement an ABC analysis approach to medical inventory management, keep the following considerations in mind.
- Get Integrated Software: Consider using specialized inventory management software that can aid in the data collection process and provide real-time insights into inventory levels. Without accurate inventory data, properly categorizing each item and tracking it with precision becomes extremely difficult. eTurns TrackStock offers various features to deliver streamlined processes and near real-time on-hand inventory data.
- Automation Tools Like Electronic Shelf Labels: In the effort to minimize the time and resources required for inventory management, relying on automation can go a long way. eTurns TrackStock offers streamlined solutions for usage tracking, customizable inventory reports, auto-replenishment orders with electronic shelf labels, and more.
- Regular Review: Implement a schedule for reviewing and updating ABC categorizations. As usage patterns change and new medical technologies emerge, ensuring that categories are up-to-date is crucial for accurate monitoring.
In conclusion, ABC analysis in conjunction with eTurns TrackStock serves as a powerful system for efficient medical inventory management. By categorizing items based on their value and significance, healthcare institutions can make informed decisions, optimize resource and labor allocation, and ensure the availability of critical medical supplies. As technology continues to advance, integrating data-driven techniques into medical inventory management will play an increasingly pivotal role in delivering quality patient care.
To learn more about how eTurns can increase the precision and efficiency of your medical inventory management practices, get in touch today.