Work Order Management Software: Use Cases and Best Practices
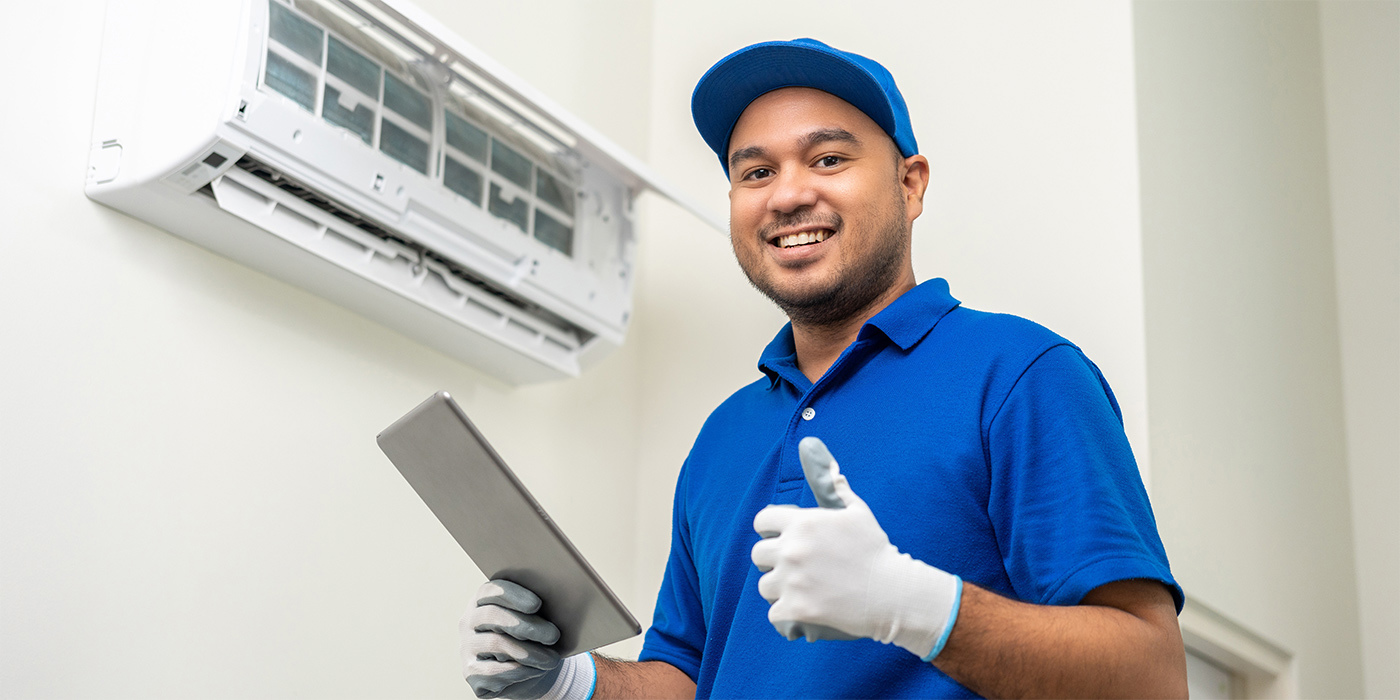
Understanding Work Order Management Software and Its Benefits
Work orders allow service teams and contractors to accurately keep track of parts used, labor hours, customer sign-off, and key details for every job. For businesses seeking a way to streamline operations, boost productivity, and enhance efficiency, adopting work order management software is critical. Work order management software offers important benefits that include:
- Enhancing asset maintenance operations
- Optimizing field service management
- Improving facility management efficiency
- Enabling auto-replenishment for materials used
- Tracking labor
- Obtaining customer sign-off
Ensure that you select work order management software that best fits your use cases and meets your needs.
Use Case 1: Enhance Maintenance Operations with Work Order Management Software
Work order management software can help improve the process of performing maintenance on crucial equipment. With work orders, organizations can more efficiently schedule and track maintenance flows for vehicles, hardware, robotics, and other physical assets.
eTurns TrackStock makes it simple to document when maintenance was performed on any given asset and to track the tools and supplies needed to do so. With up to ten user-defined fields and streamlined photo capture, maintenance teams can quickly record follow-up notes or useful information about equipment use as well.
After parts have been added to a work order, TrackStock decrements those items from on-hand inventory and triggers auto-replenishment orders if the on-hand-quantity is less than the item's minimum level.
Users can even voice a request to the eTurns app to add parts from a work order using voice recognition.
In doing so, facility maintenance software reduces downtime and ensures that equipment is well-maintained and ready to be used at any time. Manufacturing, trucking, and other machinery-heavy industries find substantial value in this use case for equipment maintenance software.
Use Case 2: Optimize Field Service Management with Work Order Management Software
Businesses in industries like utilities and construction have to accurately document and organize all aspects of field service operations. Selecting a good work order management software can optimize this process by streamlining communication, ensuring inventory stays above minimum levels, and minimize delays.
eTurns TrackStock allows field teams to add pre-configured “quicklists” of materials needed for each job and quickly scan the barcode of each additional item needed. Users can easily capture the unique attributes of any job within the app for accurate accounting, billing, and inventory management. Easily take photos of the beginning and end of a job and capture customer signatures upon job completion.
This added visibility makes it possible for field teams to complete jobs promptly and without error. Cut down on accounts receivable cycle time and integrate inventory management capabilities to ensure that stockouts never hold you back from timely job completion. eTurns TrackStock allows for smooth communication between field service teams and central office operations.
Use Case 3: Improve Facility Management Efficiency with Work Order Management Software
Facility managers must juggle maintenance needs, security, storage, space utilization and more. Using an advanced facility management software like eTurns TrackStock allows facility managers to create, assign, and monitor work orders and inventory in a centralized system.
Building mainenance techs can use work orders to manage the MRO material required to perform building maintenance.
After parts and labor have been added to a work order, TrackStock decrements those items from on-hand inventory and triggers auto-replenishment orders if the on-hand-quantity is less than the item's minimum level.
TrackStock streamlines inspections, repairs, storage allocation tasks and more within the app. With demand forecasting capabilities and an AI Min/Max Dashboard, facility managers can implement effective inventory reduction strategies. From healthcare to education, this use case for work order management software improves processes across industries.
Best Practices for Implementing and Utilizing Work Order Management Software
As you implement your routines for utilizing a new work order software solution, keep the following best practices in mind:
- Make time for thorough training. Make sure employees know how to use it, when to use it and why to use it. If they use it properly, it will end up being a tremendous value in telling you how, when, and in what way your company has performed maintenance. Present a deep dive into the benefits and abilities of the new software to ensure utmost utilization.
- Ensure all workflows are clearly defined and all formats are standardized. This aids in efficient and reliable information capture across all jobs. In TrackStock, you can customize up to ten fields to clearly outline the necessary information for each work order.
- Create a system for monitoring and analyzing all work orders. This system will be the key to continuous improvement and keep teams accountable and on time.
Selecting the Right Work Order Management Software for Your Business Needs
Choosing a work order management software that truly meets the needs of your organization is the most important factor. eTurns TrackStock makes work order management a breeze, whether you need to group together items or kits or whether your key focus is in-depth labor documentation and customer signoff. Once you’ve confirmed that a work order management software solution meets your basic requirements as far as capabilities are concerned, consider the following aspects to select the best work order software for your business:
- Flexible scanning ability: Make sure your work order’s mobile scanning software can easily recognize barcodes of any of the four common item identification: UPC, customer item number, supplier item number, manufacturer item number. Best practices are the capability to scan any one of those 4 numbers to find that particular item.
- Optimized Inventory Replenishment: Most work order software tracks items used on a job but can’t follow that up with automated replenishment orders to resupply the stockroom. eTurns work order software allows for inventory optimization based on past usage, making sure you only replenish what you need.
- Integration capabilities: Smooth adoption and integration hinges upon a software’s ability to integrate seamlessly with your other systems. Avoid redundancy and inefficient silos by selecting software that can communicate with your customer relationship management system and your enterprise resource planning tools.
- Mobile accessibility: Field and warehouse teams need to be able to quickly and easily access work orders on the go. The eTurns app offers an excellent mobile interface, including the capability to use a mobile device camera or laser scanner to capture images, videos, and other job documentation.
Select a work order management software that offers scalable and customizable solutions to fit your unique organization – like eTurns TrackStock. Our software takes the tedious steps of tracking material consumption and labor and streamlines all documentation and inventory management requirements. With auto-replenishment of the parts used, customizable fields in all orders, mobile documentation capabilities, and more, TrackStock is designed to meet the unique requirements of any industry.