How to Track and Manage Inventory Remotely: 3 Useful CMI Tips for Suppliers
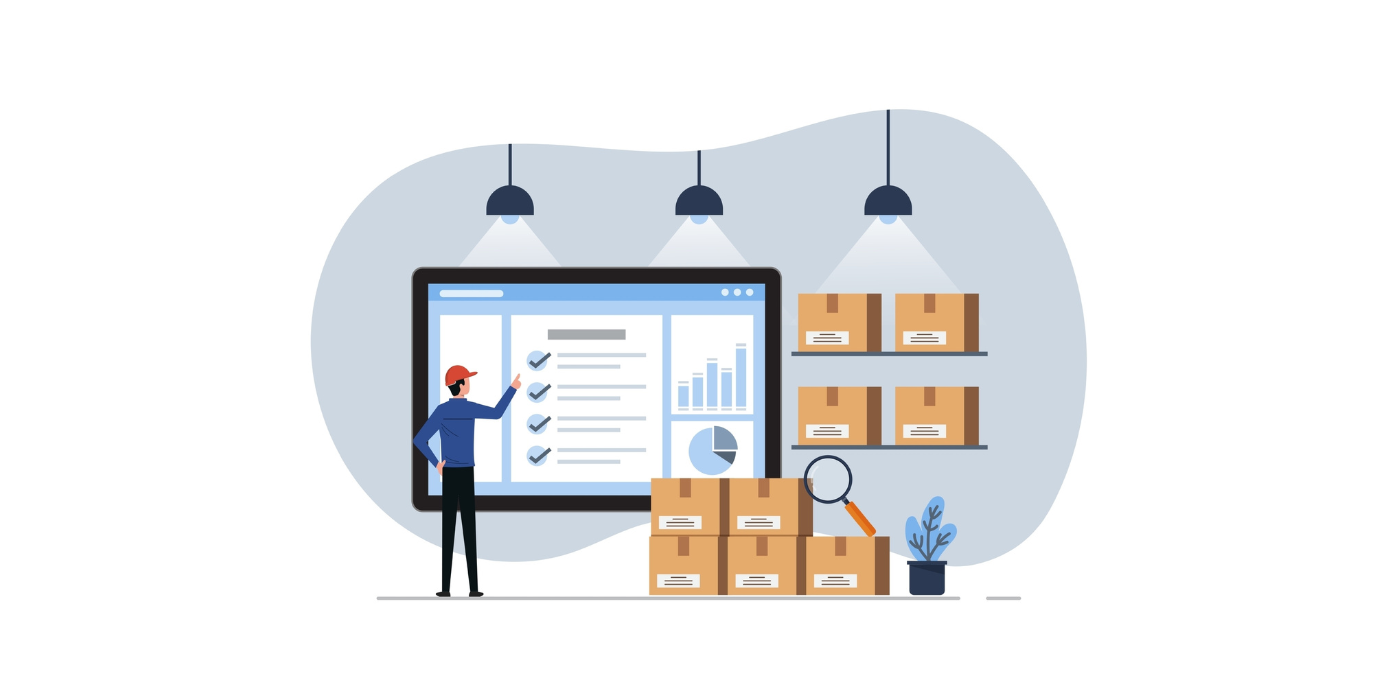
A renewed push toward cost savings is blurring the line between VMI and CMI for many suppliers. With advancements in technology, CMI apps have emerged as a game-changer for suppliers looking for remote inventory management solutions for their customers. Explore what remote inventory management is and learn three valuable tips for effectively implementing it.
What Is Remote Inventory Management?
In traditional VMI (vendor-managed inventory) relationships, a supplier representative regularly visits the customer site in order to perform inventory counts and initiate replenishment orders. This structure ideally fosters trust and loyalty between the supplier and their customer, while alleviating time-consuming inventory management tasks for the customer.
However, developments in technology have begun to displace these conventional processes and instead introduce new methods of inventory management that do not require a representative to physically visit a customer’s site. Remote inventory management refers to the process of having a supplier monitor, track, and replenish customer stockroom inventory without being onsite often, or at all.
Remote inventory management requires the use of cloud VMI/CMI software and sensor-based solutions at the point-of-use that can lend real-time insights into inventory levels, supply movement, and other critical data about customer stockroom inventory.
The point-of-use is where material gets consumed and it is always remote from the supplier.
Why Do Suppliers Need Remote Inventory Management?
One of the biggest reasons suppliers need remote inventory management is to manage consigned inventory at the customer’s point-of-use.
In this situation, a supplier owns the material that they store at the customer’s location until the customer uses it. A CMI mobile scanning app, such as TrackStock, is incredibly useful for helping the customer scan out consigned material as it is consumed. The software can deliver consolidated consumption transactions to the supplier and provide one invoice to the customer in addition to helpful reporting.
Some electrical contractors who get consigned inventory from their suppliers are even able to sell back the unused stock at the end of a job, making each job more profitable thanks to remote inventory management software for consignment inventory.
3 Tips for Remote Inventory Management and Tracking
1. Utilize cloud-based inventory management software
Cloud-based inventory management software can remotely manage inventory in a CMI model. The customer can use a CMI inventory app to scan out an item from on-hand inventory, to cycle count items, or to scan-to-order. Previously set min/max levels for each item will trigger replenishment as needed and the supplier can remotely monitor this process from offsite.
Remote inventory management solutions like eTurns TrackStock offer several advantages, including:
- Visibility to near real-time inventory data
- Auto-replenishment based on min/max levels
- A Min/Max Tuning Dashboard that guides you to optimized inventory levels
With this software, suppliers and their customers can access point-of-use customer inventory information from anywhere with an internet connection, enabling quick decision-making and improved collaboration with customers.
2. Implement QR code or electronic shelf label technology for CMI self-service inventory replenishment
Providing a fast and easy way for customers to place self-service replenishment orders helps strengthen customer relationships and facilitate timely orders.
QR code scanning: By scanning QR codes on product bins using phones or ruggedized PDAs, inventory managers can initiate the replenishment process using the TrackStock app. One scan with the app tracks vital info like package quantity, bin location, supplier id, etc. Plus, TrackStock knows the min/max level for each item and will trigger automated replenishment orders when the inventory count goes below the minimum level.
Electronic Shelf Labels: Electronic Shelf Labels have a button that triggers immediate digital orders in a CMI model. When the user has visually confirmed that the reorder point has been reached, he pushes the button to send a digital order to the supplier that has been designated during the set-up process in the TrackStock software. eLabels display important information such as minimum/maximum levels, par levels (reorder points), and on-hand inventory levels. TrackStock prevents duplicate replenishment orders from multiple button pushes.
These methods of remote inventory management and replenishment save time for suppliers and customers alike while preventing stockouts and manual errors.
3. Implement remote tracking technologies like SensorBins, RFID and BoxLock
The Internet of Things (IoT) has revolutionized inventory management by enabling remote tracking of inventory in real-time. IoT devices, such as RFID tags and sensors can be attached to products or storage locations to monitor their movement, temperature, weight, and more.
For example, eTurns SensorBins use weight sensors for inventory management by converting bin weights into item quantities. This technology allows for ongoing inventory counts and automatic replenishment orders with no human intervention required.
Boxlock technology creates secure, trackable remote access capabilities. Boxlocks are secure and rugged smart locks with integrated barcode scanners and real-time connectivity. They have the flexibility to protect and track critical assets remotely.
By leveraging the latest tools for remote inventory management, suppliers can provide a streamlined self-service option for their customers without sacrificing excellent customer service. Get in touch to learn how eTurns can help you implement remote inventory management software.